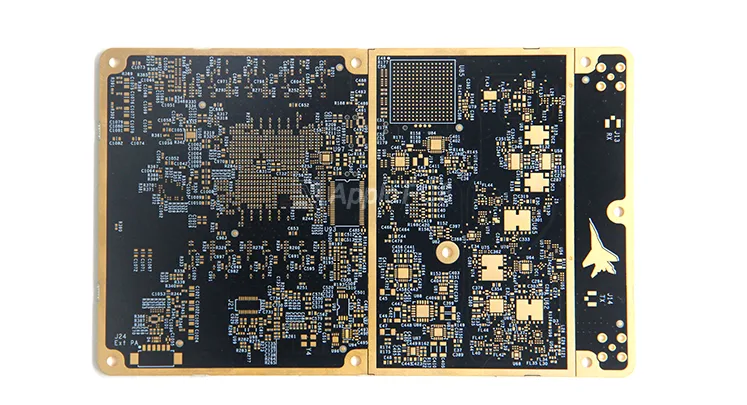
Traditional FR4 PCBs are limited by their low thermal conductivity and thermal expansion mismatch issues, making them highly prone to component failure in high-temperature, high-power scenarios. Ceramic substrates are emerging as the key material to overcome these limitations due to their unique performance advantages. Their thermal conductivity can exceed that of FR4 by over a hundredfold while offering excellent insulation strength and a thermal expansion coefficient that matches that of chips. The two most common ceramic PCB materials currently on the market are aluminum oxide (Al₂O₃) and aluminum nitride (AlN), each with distinct advantages suited to different applications.
Aluminum Oxide PCB
Among ceramic PCB substrate materials, Al₂O₃, particularly the 96% pure form, is currently the most common. It is an excellent natural electrical insulator with stable thermal properties and a thermal conductivity coefficient of approximately 24 W/m·K. This coefficient is significantly higher than that of common metal-based PCB materials. While not as effective as AIN PCBs in terms of thermal conductivity, Al₂O₃ PCBs are widely used due to their cost-effectiveness and reliable performance.
Additionally, a high-purity version, 99.6% Al₂O₃, has a thermal conductivity of approximately 29 W/m·K, making it more advantageous for applications requiring higher heat dissipation efficiency. Due to its high light reflectance and good heat dissipation capabilities, Al₂O₃ PCBs are particularly suitable for optoelectronic applications, such as LED lighting. Its low thermal expansion coefficient and low signal loss also enable it to perform well in sensor modules, high-frequency systems, and heat dissipation modules.
Aluminum Nitride PCB
Compared to traditional Al₂O₃ ceramic PCBs, AIN PCBs have the advantage of extremely high thermal conductivity, typically reaching 170-200 W/m·K—far superior to Al₂O₃. This excellent thermal conductivity enables the PCB to rapidly conduct the heat generated by electronic components, making it ideal for high-power electronic systems.
In addition to its powerful heat conduction performance, the AlN material itself has excellent electrical insulation properties. These properties can effectively prevent interference between circuits, ensuring the safety and stability of circuit operation while achieving efficient heat dissipation. Despite their relatively high cost, AIN PCBs are widely used in precision electronics, electric vehicles, laser equipment, radar systems, aerospace, and other fields because these industries have extremely high requirements for thermal management and reliability.
Comparison of AlN and Al₂O₃ PCB Properties
Aluminum nitride ceramics are based on a hexagonal crystal structure and consist of a strong covalent bond network. Al₂O₃ ceramics are based on a hexagonal close-packed structure. The structural differences between the two types of ceramic substrates directly determine their performance boundaries. The table below compares the specific properties of the two in detail.
Property | Al2O3 (96%) | AlN | Unit |
Thermal Conductivity | 24 | 180 | W/mK |
CTE | 6.7 | 4.6 | x 10-6/K |
Dielectric Constant | 9.8 | 9 | – |
Signal Loss | 0.2 | 0.2 | x 10-3 |
Light Reflectivity | 70/85 | 35 | % |
Dielectric Strength | ≥15 | ≥15 | KV/mm |
Rupture Strength | 400 | 450 | Mpa |
Advantages of Aluminum Oxide PCBs
- Strong electrical insulation: Suitable for high-voltage circuits, effectively ensuring system safety.
- Stable thermal performance: Thermal conductivity can reach 25–30 W/m·K, meeting medium-power heat dissipation requirements.
- Good environmental resistance: Excellent moisture resistance, corrosion resistance, and chemical resistance.
- Cost and Production Efficiency Advantages: Stable raw material supply and mature manufacturing processes offer high cost-effectiveness.
- Strong process compatibility: Seamlessly compatible with thick film technology and DBC (direct bond copper) processes.
- Good precision adaptability: Supports high-resolution graphic printing, suitable for compact circuit design.
Limitations of Aluminum Oxide Ceramic PCBs
- Average thermal conductivity: Compared to high-end ceramics such as AlN, the thermal conductivity coefficient is relatively low, resulting in limited heat dissipation capabilities.
- Brittle material: Prone to damage from external impacts or drops, requiring stringent assembly and transportation standards.
- High thermal expansion coefficient: Poor compatibility with silicon chips, potentially causing thermal stress concentration.
- Limited high-frequency performance: Unsuitable for ultra-high-frequency or high-speed switching RF or microwave circuits.
- Surface flatness variations: Subject to certain process control limitations, minor flatness errors may occur.
Advantages of Aluminum Nitride PCBs
- Extremely high thermal conductivity: Thermal conductivity typically exceeds 170 W/m·K, far surpassing traditional ceramics and metal substrates.
- Superior high-frequency performance: Features low dielectric loss, effectively maintaining the integrity of high-frequency signals.
- Excellent mechanical strength and thermal shock stability: Enhances PCB reliability in high-temperature fluctuating environments.
- Coefficient of thermal expansion (CTE): Well-matched with silicon chips, helping to reduce thermal stress and enhance overall package stability;
- Superior electrical insulation performance: Capable of safely withstanding high-voltage operating conditions.
- Supports advanced packaging technologies: Including on-board chip (OBO) and system-in-package (SiP).
Limitations of Aluminum Nitride PCBs
Although aluminum nitride ceramic PCBs offer numerous advantages, they also present certain challenges in practical applications:
- High manufacturing costs: Due to the high cost of raw materials and complex processing techniques, the overall production cost of AlN PCBs is significantly higher than that of aluminum oxide.
- High manufacturing requirements: The process equipment, process control, and technical proficiency of personnel must meet stringent standards, and non-standardized production lines may struggle to ensure consistent quality.
- Brittle material: Although aluminum nitride has better mechanical strength than aluminum oxide, the ceramic material itself is hard and brittle. Stress concentration must be avoided during processing and assembly to prevent cracking.
- Difficult processing: AlN causes severe tool wear, increasing challenges in production maintenance and cost control.
- Process compatibility issues: Without customized matching, some traditional metal slurries may have poor compatibility with AlN substrates.
- Supply chain constraints: Aluminum nitride material supply is relatively tight, with limited production capacity, leading to longer delivery cycles.
What Should I Choose Between Al₂O₃ and AlN Ceramic Substrate?
When selecting a ceramic PCB substrate, three factors should be considered comprehensively:
- Performance requirements: Are there high heat flux, high frequency, or high voltage specifications?
- Cost factors: Is the project aimed at the mass market, or is it a small-batch customized product?
- Expected lifespan and reliability: Is long-term stable operation and critical function assurance required?
If your circuit generates moderate heat and the project prioritizes cost-effectiveness and the feasibility of large-scale production, Al₂O₃PCB is a more attractive option. It offers stable thermal conductivity and excellent insulation properties, making it suitable for most general-purpose electronic products, such as LED lighting, consumer electronics, and medium-power modules. Additionally, alumina materials are widely available, and the manufacturing process is highly standardized, enabling seamless integration into existing production lines and processes.
However, if you are dealing with power-intensive designs, such as RF power modules, electric vehicle controllers, high-power LED arrays, or precision laser systems, then AlN PCBs are a more worthwhile investment. They offer excellent thermal efficiency and thermal expansion matching, which helps extend component lifespan.
Once these basic parameters are clarified, selecting the appropriate ceramic substrate typically becomes straightforward. If you remain uncertain about which ceramic PCB material best suits your application, please feel free to contact ApplePCB. With over 15 years of specialized experience in ceramic PCB manufacturing, we can provide professional material selection recommendations, sample verification, and mass production support tailored to your product requirements.